Functionalization of Additively Manufactured Hot Stamping Tools Using Ball Burnishing
- Profil- und Blechumformung
- ReGAT
- Umformtechnische Grundlagenforschung
- Technologieentwicklung
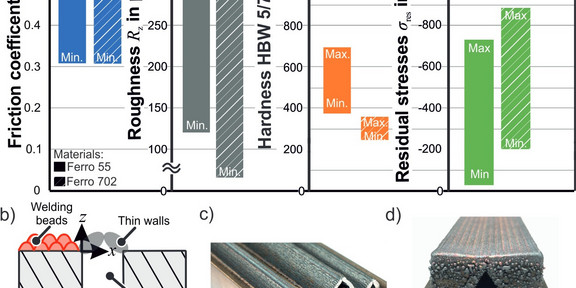
Funding | German Research Foundation (DFG) |
Project | 417202720 |
Contact | Anna Komodromos M. Sc. |
Hot stamping is used in sheet metal forming in order to exploit the increase in strength due to quenching. For this purpose, cooling channels, which are usually produced using machining processes, are integrated in the tools. The production of hot stamping tools using directed energy deposition (DED) is intended to enable the channels to be positioned close to the surface. Therefore, the properties of the additively manufactured surfaces in terms of roughness, hardness, friction, and residual stresses are first characterized (see Figure a). The initially rough surface after DED is then leveled by ball burnishing. This induces compressive residual stresses, which increase with higher rolling pressures. To manufacture the cooling channels, open cooling channel structures are milled into a solid material and then sealed using DED (see Figure b-d). When designing the cooling channels it is necessary to achieve a compromise between the additive manufacturability and the surface fraction, which effectively contributes to the heat balance on the tool surface.