Composite Cold Forging of Cold-Forged Semi-Finished Parts
- Massivumformung
- Umformtechnische Grundlagenforschung
- Technologieentwicklung
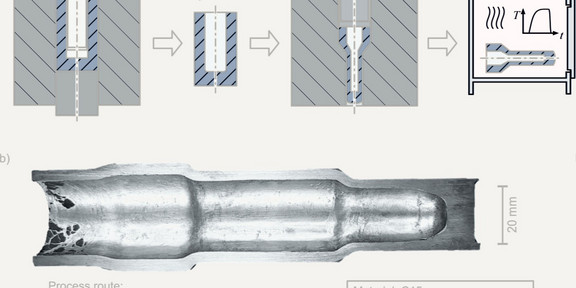
Funding | Germand Research Foundation (DFG) |
Project | 270149504 |
Contact | Robin Gitschel M. Sc. |
Status | Completed |
Composite cold forging enables the production of material composites by cold forging. In this process, backward can extrusion is used to produce semi-finished product geometries. In a subsequent process step, a core material is inserted into the semi-finished can. Subsequently, this composite billet is formed by forward rod extrusion to join both materials and produce a hybrid shaft (Figure a). By combining materials with different physical properties, the lightweight potential can be increased or additional functions can be integrated. Through experimental as well as numerical investigations, general design guidelines for the successful manufacture of composite shafts were derived. Since heat treatment often takes place between or after forming in cold forging, heat treatment concepts for steel-aluminum composite shafts were investigated. For long dwell times above the melting temperature of the core material, the core can be removed by melting so that heat-treated hollow shafts can be produced (Figure b).