Projects
Basic research on forming technology
Forming of Additively Manufactured Sandwich Sheets with Optimized Core Structures
- Materialcharakterisierung
- Technologieentwicklung
- ReGAT
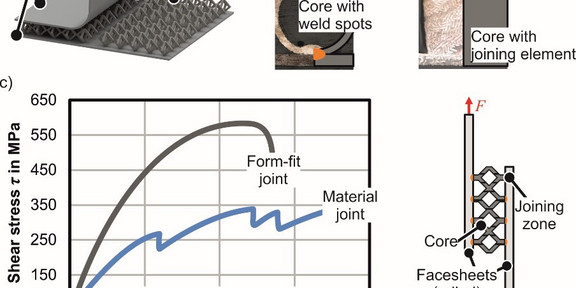
Funding | German Research Foundation (DFG) |
Project | 317137194 |
Contact | Stephan Rosenthal M. Sc. |
In cooperation with the Institute of Product Engineering at the University of Duisburg-Essen, sandwich sheet composites with core structures optimized for forming are being developed. The additively manufactured core is joined with rolled cover sheets and enables the production of load-adapted semi-finished products to overcome the build-space restrictions of additive manufacturing machines. For composite manufacturing form-fit and material-fit processes are characterized in terms of their suitability for a subsequent forming operation by means of shear tests. The material bond is achieved by local welding of weld spots and cover sheets with short high-current pulses. In particular, the identification of the process parameters plays a central role. A form-fit connection is produced by a trunnion joint with trunnion geometries optimized for forming. Shear tests show a higher strength in favor of the form-fit connection (see figure). Improvements in the welding process are expected to enhance the performance of the material-joint connection.
Material characterization
Forming of Additively Manufactured Sandwich Sheets with Optimized Core Structures
- Materialcharakterisierung
- Technologieentwicklung
- ReGAT
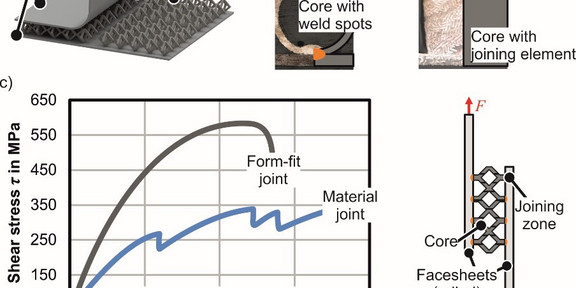
Funding | German Research Foundation (DFG) |
Project | 317137194 |
Contact | Stephan Rosenthal M. Sc. |
In cooperation with the Institute of Product Engineering at the University of Duisburg-Essen, sandwich sheet composites with core structures optimized for forming are being developed. The additively manufactured core is joined with rolled cover sheets and enables the production of load-adapted semi-finished products to overcome the build-space restrictions of additive manufacturing machines. For composite manufacturing form-fit and material-fit processes are characterized in terms of their suitability for a subsequent forming operation by means of shear tests. The material bond is achieved by local welding of weld spots and cover sheets with short high-current pulses. In particular, the identification of the process parameters plays a central role. A form-fit connection is produced by a trunnion joint with trunnion geometries optimized for forming. Shear tests show a higher strength in favor of the form-fit connection (see figure). Improvements in the welding process are expected to enhance the performance of the material-joint connection.
Technology development
Forming of Additively Manufactured Sandwich Sheets with Optimized Core Structures
- Materialcharakterisierung
- Technologieentwicklung
- ReGAT
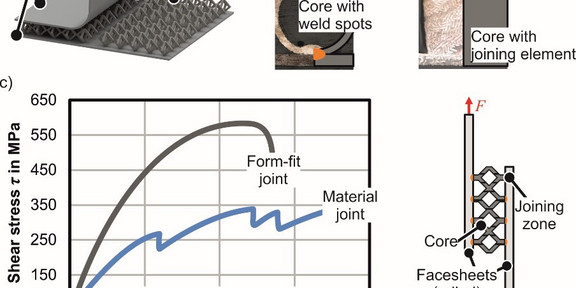
Funding | German Research Foundation (DFG) |
Project | 317137194 |
Contact | Stephan Rosenthal M. Sc. |
In cooperation with the Institute of Product Engineering at the University of Duisburg-Essen, sandwich sheet composites with core structures optimized for forming are being developed. The additively manufactured core is joined with rolled cover sheets and enables the production of load-adapted semi-finished products to overcome the build-space restrictions of additive manufacturing machines. For composite manufacturing form-fit and material-fit processes are characterized in terms of their suitability for a subsequent forming operation by means of shear tests. The material bond is achieved by local welding of weld spots and cover sheets with short high-current pulses. In particular, the identification of the process parameters plays a central role. A form-fit connection is produced by a trunnion joint with trunnion geometries optimized for forming. Shear tests show a higher strength in favor of the form-fit connection (see figure). Improvements in the welding process are expected to enhance the performance of the material-joint connection.
Industry-related research
Forming of Additively Manufactured Sandwich Sheets with Optimized Core Structures
- Materialcharakterisierung
- Technologieentwicklung
- ReGAT
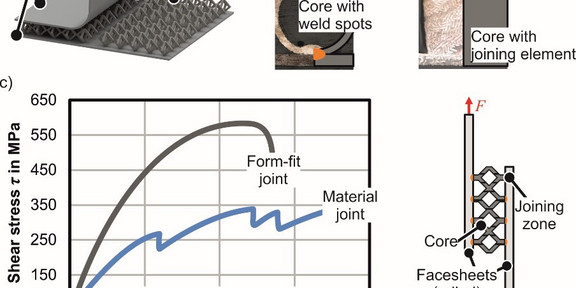
Funding | German Research Foundation (DFG) |
Project | 317137194 |
Contact | Stephan Rosenthal M. Sc. |
In cooperation with the Institute of Product Engineering at the University of Duisburg-Essen, sandwich sheet composites with core structures optimized for forming are being developed. The additively manufactured core is joined with rolled cover sheets and enables the production of load-adapted semi-finished products to overcome the build-space restrictions of additive manufacturing machines. For composite manufacturing form-fit and material-fit processes are characterized in terms of their suitability for a subsequent forming operation by means of shear tests. The material bond is achieved by local welding of weld spots and cover sheets with short high-current pulses. In particular, the identification of the process parameters plays a central role. A form-fit connection is produced by a trunnion joint with trunnion geometries optimized for forming. Shear tests show a higher strength in favor of the form-fit connection (see figure). Improvements in the welding process are expected to enhance the performance of the material-joint connection.
Completed Projects
Forming of Additively Manufactured Sandwich Sheets with Optimized Core Structures
- Materialcharakterisierung
- Technologieentwicklung
- ReGAT
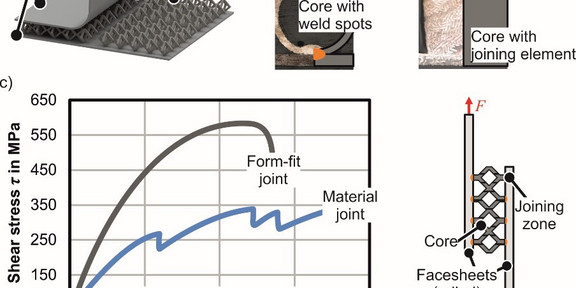
Funding | German Research Foundation (DFG) |
Project | 317137194 |
Contact | Stephan Rosenthal M. Sc. |
In cooperation with the Institute of Product Engineering at the University of Duisburg-Essen, sandwich sheet composites with core structures optimized for forming are being developed. The additively manufactured core is joined with rolled cover sheets and enables the production of load-adapted semi-finished products to overcome the build-space restrictions of additive manufacturing machines. For composite manufacturing form-fit and material-fit processes are characterized in terms of their suitability for a subsequent forming operation by means of shear tests. The material bond is achieved by local welding of weld spots and cover sheets with short high-current pulses. In particular, the identification of the process parameters plays a central role. A form-fit connection is produced by a trunnion joint with trunnion geometries optimized for forming. Shear tests show a higher strength in favor of the form-fit connection (see figure). Improvements in the welding process are expected to enhance the performance of the material-joint connection.