Projects
Basic research on forming technology
Optimized Working Coil Windings for Electromagnetic Forming Employing Additive Manufacturing Techniques
- Sonderverfahren
- Technologieentwicklung
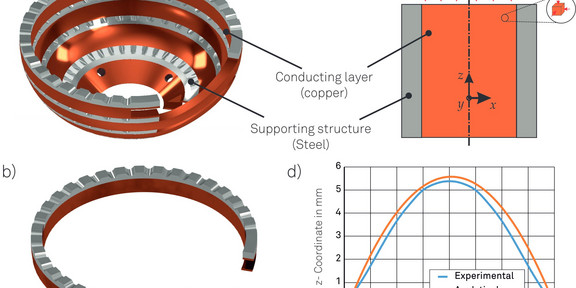
Funding | German Research Foundation (DFG) |
Project | 259797904 |
Contact | Siddhant Prakash Goyal M. Sc. |
In collaboration with the Institute of Machine Tools and Factory Manage-ment (IWF) of TU Berlin, the project was conducted with the objective of investigating hybrid (multi-metallic) additively manufactured coils for electromagnetic forming for an increased tool life. The focus of research at the IUL was to study the parameters increasing the tool life, e.g. hybrid coils (see Figure a, b, and c). Due to the complex geometry of the hybrid coils, an assembly-based solution was proposed and developed which provides additional flexibility to the coil use. The reduction of plastification of the coil conductor was a further attempt using steel support elements on the sides. With this, a hydrostatic pressure in the coil is applied (see Figure c). Also, a semi-analytical computation method was elaborated to reduce the design effort compared to using coupled numerical simulations for complex multi-winding geometries. From the experiments the geometry of the coil and the workpiece were measured and compared to the introduced efficient computation method (see Figure d).
Material characterization
Optimized Working Coil Windings for Electromagnetic Forming Employing Additive Manufacturing Techniques
- Sonderverfahren
- Technologieentwicklung
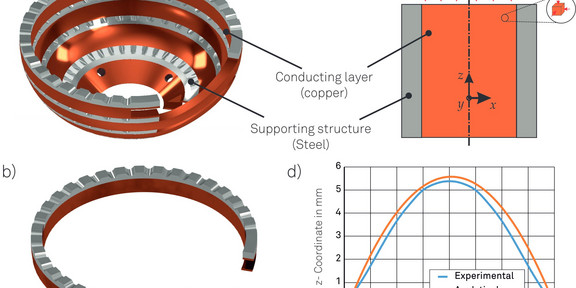
Funding | German Research Foundation (DFG) |
Project | 259797904 |
Contact | Siddhant Prakash Goyal M. Sc. |
In collaboration with the Institute of Machine Tools and Factory Manage-ment (IWF) of TU Berlin, the project was conducted with the objective of investigating hybrid (multi-metallic) additively manufactured coils for electromagnetic forming for an increased tool life. The focus of research at the IUL was to study the parameters increasing the tool life, e.g. hybrid coils (see Figure a, b, and c). Due to the complex geometry of the hybrid coils, an assembly-based solution was proposed and developed which provides additional flexibility to the coil use. The reduction of plastification of the coil conductor was a further attempt using steel support elements on the sides. With this, a hydrostatic pressure in the coil is applied (see Figure c). Also, a semi-analytical computation method was elaborated to reduce the design effort compared to using coupled numerical simulations for complex multi-winding geometries. From the experiments the geometry of the coil and the workpiece were measured and compared to the introduced efficient computation method (see Figure d).
Technology development
Optimized Working Coil Windings for Electromagnetic Forming Employing Additive Manufacturing Techniques
- Sonderverfahren
- Technologieentwicklung
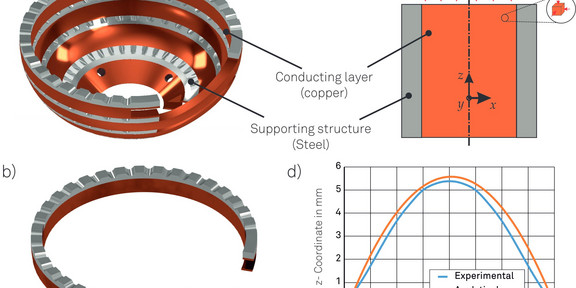
Funding | German Research Foundation (DFG) |
Project | 259797904 |
Contact | Siddhant Prakash Goyal M. Sc. |
In collaboration with the Institute of Machine Tools and Factory Manage-ment (IWF) of TU Berlin, the project was conducted with the objective of investigating hybrid (multi-metallic) additively manufactured coils for electromagnetic forming for an increased tool life. The focus of research at the IUL was to study the parameters increasing the tool life, e.g. hybrid coils (see Figure a, b, and c). Due to the complex geometry of the hybrid coils, an assembly-based solution was proposed and developed which provides additional flexibility to the coil use. The reduction of plastification of the coil conductor was a further attempt using steel support elements on the sides. With this, a hydrostatic pressure in the coil is applied (see Figure c). Also, a semi-analytical computation method was elaborated to reduce the design effort compared to using coupled numerical simulations for complex multi-winding geometries. From the experiments the geometry of the coil and the workpiece were measured and compared to the introduced efficient computation method (see Figure d).
Industry-related research
Optimized Working Coil Windings for Electromagnetic Forming Employing Additive Manufacturing Techniques
- Sonderverfahren
- Technologieentwicklung
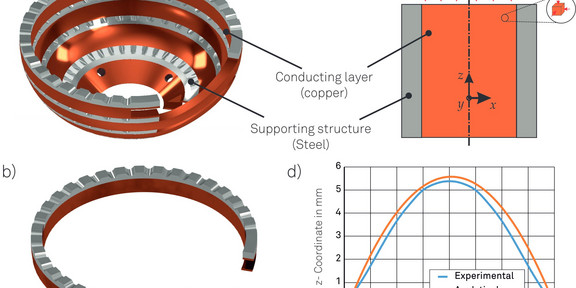
Funding | German Research Foundation (DFG) |
Project | 259797904 |
Contact | Siddhant Prakash Goyal M. Sc. |
In collaboration with the Institute of Machine Tools and Factory Manage-ment (IWF) of TU Berlin, the project was conducted with the objective of investigating hybrid (multi-metallic) additively manufactured coils for electromagnetic forming for an increased tool life. The focus of research at the IUL was to study the parameters increasing the tool life, e.g. hybrid coils (see Figure a, b, and c). Due to the complex geometry of the hybrid coils, an assembly-based solution was proposed and developed which provides additional flexibility to the coil use. The reduction of plastification of the coil conductor was a further attempt using steel support elements on the sides. With this, a hydrostatic pressure in the coil is applied (see Figure c). Also, a semi-analytical computation method was elaborated to reduce the design effort compared to using coupled numerical simulations for complex multi-winding geometries. From the experiments the geometry of the coil and the workpiece were measured and compared to the introduced efficient computation method (see Figure d).
Completed Projects
Optimized Working Coil Windings for Electromagnetic Forming Employing Additive Manufacturing Techniques
- Sonderverfahren
- Technologieentwicklung
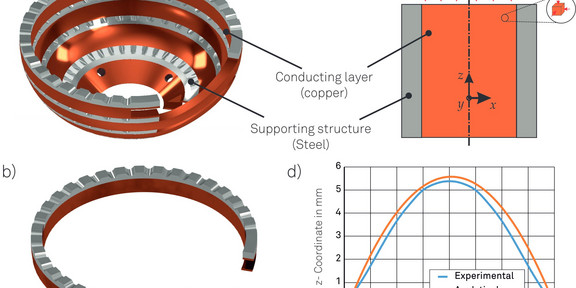
Funding | German Research Foundation (DFG) |
Project | 259797904 |
Contact | Siddhant Prakash Goyal M. Sc. |
In collaboration with the Institute of Machine Tools and Factory Manage-ment (IWF) of TU Berlin, the project was conducted with the objective of investigating hybrid (multi-metallic) additively manufactured coils for electromagnetic forming for an increased tool life. The focus of research at the IUL was to study the parameters increasing the tool life, e.g. hybrid coils (see Figure a, b, and c). Due to the complex geometry of the hybrid coils, an assembly-based solution was proposed and developed which provides additional flexibility to the coil use. The reduction of plastification of the coil conductor was a further attempt using steel support elements on the sides. With this, a hydrostatic pressure in the coil is applied (see Figure c). Also, a semi-analytical computation method was elaborated to reduce the design effort compared to using coupled numerical simulations for complex multi-winding geometries. From the experiments the geometry of the coil and the workpiece were measured and compared to the introduced efficient computation method (see Figure d).