Entwicklung eines Modells zur Vorhersage der Geometrieänderungen bei der Federherstellung auf Basis der Plastizitätstheorie unter Berücksichtigung der Wärmebehandlung
- Profil- und Blechumformung
- Umformtechnische Grundlagenforschung
- Materialcharakterisierung
- Industrienahe Forschung
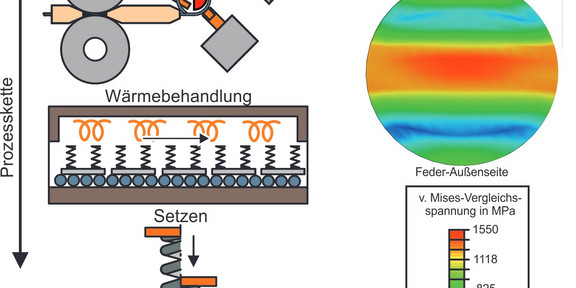
Projektträger | AiF / IGF |
Projektnummer | IGF 21490 N |
Kontakt | Philipp Rethmann M. Sc. |
Die Herstellung von Schraubendruckfedern erfolgt in einer Prozesskette aus Winden, Wärmebehandeln und Vorsetzen (vgl. Bild a). Bei der Umformung des Federdrahts im Windeautomat werden dabei Eigenspannungen erzeugt (vgl. Bild b). Die thermisch induzierte Absenkung der Fließspannung bei der folgenden Wärmebehandlung bewirkt einen teilweisen Abbau dieser Eigenspannungen und eine Änderung der Federmaße. Im abschließenden Schritt des Vorsetzens erfolgt eine plastische Belastung der Feder, sodass die Länge abnimmt und Torsionseigenspannungen eingebracht werden. Großen Einfluss auf die Eigenspannungen und die Formänderungen haben die Werkstoffeigenschaften der Federdrähte, die prozessnah durch Zug- und Torsionsversuche ermittelt werden. Auf der Basis von experimentellen und numerischen Untersuchungen der Teilprozesse wird ein (halb)-analytisches Prozessmodell entwickelt, mit dem die Beschreibung der Geometrieänderungen möglich ist. Dieses Modell kann zur Unterstützung des Einrichtprozesses von Federwindeautomaten eingesetzt werden.